Using a helical worm gear motor in wastewater treatment applications requires careful consideration of several design factors to ensure reliable and efficient operation in a challenging environment. Here are the main design considerations:
1. Corrosion Resistance: Wastewater treatment facilities are exposed to corrosive substances. Select materials for the gear motor, housing, and seals that are highly resistant to corrosion. Stainless steel and corrosion-resistant coatings can be beneficial.
2. Sealing and Ingress Protection: Ensure that the gear motor has a high level of ingress protection (IP) to prevent water and contaminants from entering the housing. IP ratings of IP65 or higher are often required.
3. Chemical Compatibility: Consider the compatibility of the gear motor materials with the chemicals used in the wastewater treatment process. Specialized coatings or materials may be needed to withstand exposure to aggressive chemicals.
4. Temperature Resistance: Wastewater can vary in temperature. Ensure that the gear motor can operate within the temperature range encountered in your specific application. Use appropriate lubricants for the temperature conditions.
5. Efficiency: Select a helical worm gear motor with good mechanical efficiency to minimize energy consumption and reduce operating costs. High-efficiency models can help save energy in continuous wastewater treatment processes.
6. Motor Protection: Incorporate motor protection features such as thermal overload protection and overcurrent protection to safeguard the motor from overheating or damage due to electrical faults.
7. Shaft Sealing: Ensure that the motor's output shaft is properly sealed to prevent water and contaminants from entering the motor and gearbox, which can lead to premature wear and failure.
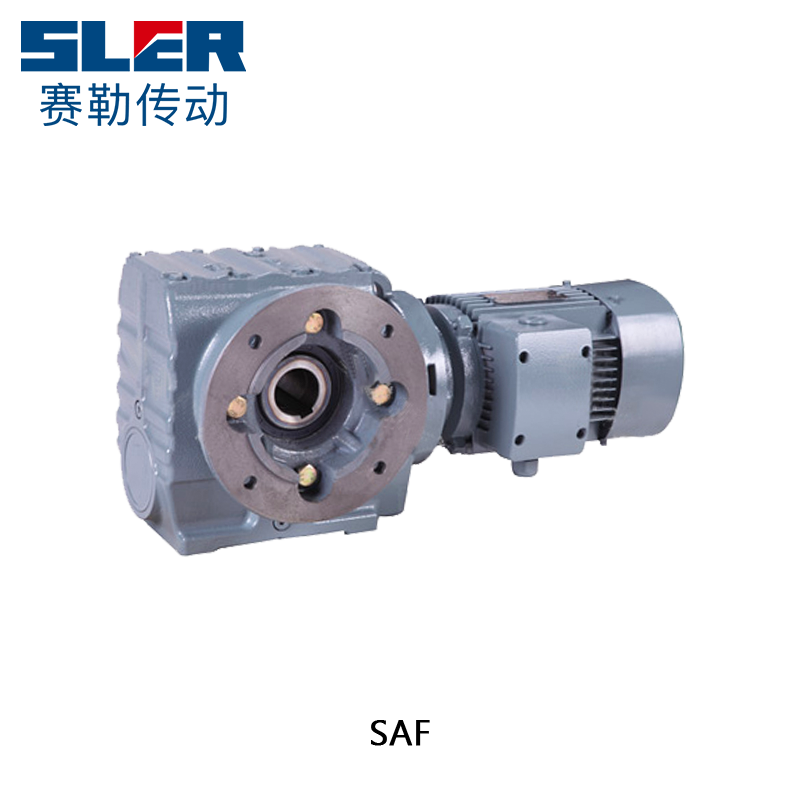
8. Mounting and Positioning: Properly mount the gear motor in a way that prevents water pooling and allows for drainage. Position it to avoid direct exposure to water jets or splashes.
9. Load and Torque Requirements: Calculate the torque and load requirements for your specific wastewater treatment application. Choose a gear motor with sufficient torque and load-bearing capacity to meet these requirements.
10. Speed Control: If precise speed control is needed, consider gear motors with variable speed options, such as frequency inverters or variable frequency drives (VFDs), to adapt to changing process conditions.
11. Maintenance Accessibility: Ensure that the gear motor is designed for easy access and maintenance. Quick and convenient access to internal components can reduce downtime for repairs and servicing.
12. Vibration and Shock Resistance: Wastewater treatment equipment can experience vibration and shock loads. Choose a gear motor with good shock and vibration resistance to withstand these conditions.
13. Environmental Regulations: Ensure compliance with environmental regulations and safety standards relevant to wastewater treatment equipment. This includes electrical safety and environmental impact considerations.
14. Backup Systems: Consider redundancy or backup systems for critical wastewater treatment processes to minimize downtime in case of gear motor failure.
15. Monitoring and Control: Implement monitoring and control systems to keep track of gear motor performance, temperature, and other parameters. This can help with preventive maintenance and early detection of issues.
By carefully considering these design factors, you can select and implement a helical worm gear motor that is well-suited to the demanding conditions of wastewater treatment applications, ensuring reliable and efficient operation while minimizing maintenance and downtime.