Using Computational Fluid Dynamics (CFD) to monitor the lubricant and noise reduction effects in a Worm Gear Speed Reducer involves simulating the fluid behavior, lubricant distribution, and noise generation within the gear system. Here's a step-by-step approach:
1. Model Creation:
- Develop a detailed 3D model of the worm gear speed reducer, including gears, housing, lubrication channels, and any seals.
- Specify accurate dimensions, material properties, gear tooth profiles, and surface finishes.
2. Fluid Domain Definition:
- Define the fluid domain encompassing the lubrication channels, including the gear mesh area, bearing spaces, and other fluid flow paths.
- Specify boundary conditions, such as inlet and outlet locations and fluid properties (density, viscosity, etc.).
3. Lubrication Analysis:
- Simulate the flow of lubricant within the gear system under various operating conditions.
- Observe lubricant distribution patterns, flow velocities, pressure distributions, and heat dissipation across the gears.
4. Lubricant Properties:
- Consider the properties of the lubricant, including viscosity, density, and thermal conductivity, to accurately model its behavior.
5. Noise Generation Analysis:
- Incorporate noise prediction capabilities into the CFD analysis.
- Simulate the interaction of lubricant flow, gear meshing, and mechanical vibrations to predict noise levels generated by the gear system.
6. Tribology Analysis:
- Incorporate tribological models to study friction and wear behavior at gear interfaces.
- Analyze how lubricant properties and flow impact frictional losses, wear, and consequently, noise generation.
7. Visualization and Analysis:
- Use CFD software to visualize lubricant flow patterns, pressure distributions, and any turbulent regions.
- Analyze results to identify areas of inadequate lubrication, excessive pressure, or flow restrictions that might contribute to noise and wear.
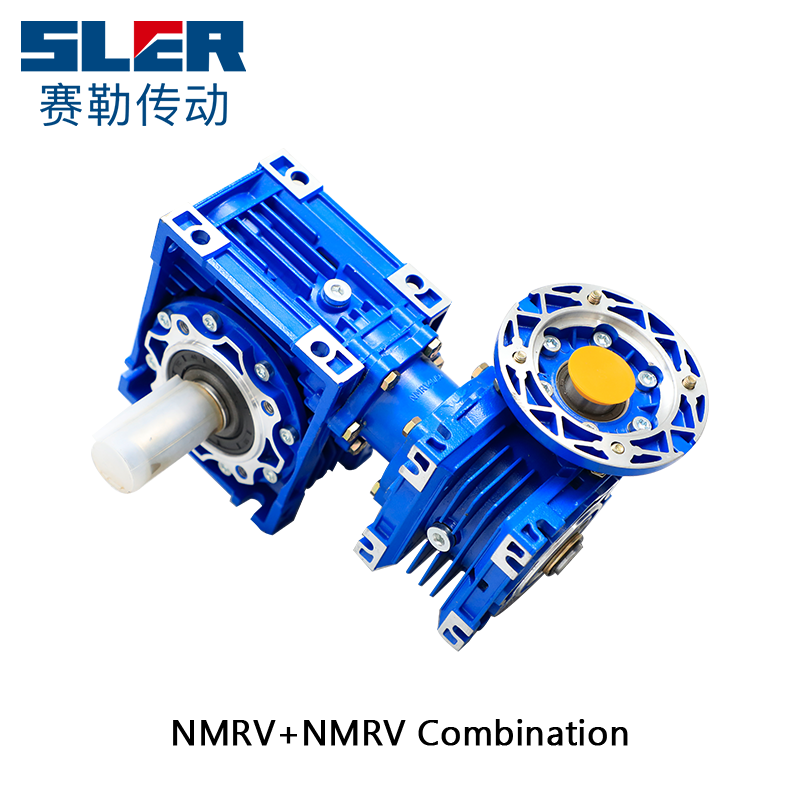
8. Noise Reduction Strategies:
- Implement virtual design changes, such as modifying gear tooth profiles, housing geometry, or lubrication pathways, to evaluate their impact on noise reduction.
- Study the effect of noise-damping coatings or additives in the lubricant.
9. Comparative Analysis:
- Compare different lubricant types, viscosities, or additives to understand their impact on lubrication effectiveness and noise generation.
10. Validation:
- Validate the CFD results against experimental data or empirical correlations to ensure accuracy and reliability.
11. Iterative Optimization:
- Iterate the simulation by adjusting parameters, materials, or designs to identify the optimal configuration for reduced noise and efficient lubrication.
12. Sensitivity Analysis:
- Perform sensitivity analysis to understand the impact of variations in operating conditions, such as load, speed, and temperature, on lubrication and noise.