Lubrication plays a crucial role in minimizing noise and vibration in worm gear speed reducers. Proper lubrication reduces friction, wear, and heat generation, leading to smoother operation and quieter performance. The choice of lubrication strategy and lubricant type depends on factors such as the application requirements, operating conditions, gear materials, and load characteristics. Here are some recommended lubrication strategies and lubricants:
1. Lubricant Type: High-quality synthetic lubricants are often recommended for worm gear speed reducers. Synthetic lubricants offer superior viscosity stability, thermal resistance, and wear protection, which contribute to quieter operation.
2. Viscosity Selection: Choosing the right viscosity grade based on the operating temperature and speed range is crucial. A lubricant with the appropriate viscosity maintains a fluid film between gear teeth, reducing direct metal-to-metal contact and dampening vibrations.
3. Additive Package: Lubricants with anti-wear, extreme pressure (EP), and anti-foaming additives help protect gear surfaces, minimize wear, and prevent foam formation, contributing to smooth and quiet operation.
4. Noise-Damping Additives: Some lubricants are formulated with noise-damping additives that help absorb vibrations and reduce noise generation during gear meshing.
5. Solid Lubricants: Lubricants containing solid additives, such as molybdenum disulfide (MoS2) or PTFE, can provide additional boundary lubrication and reduce friction-induced noise.
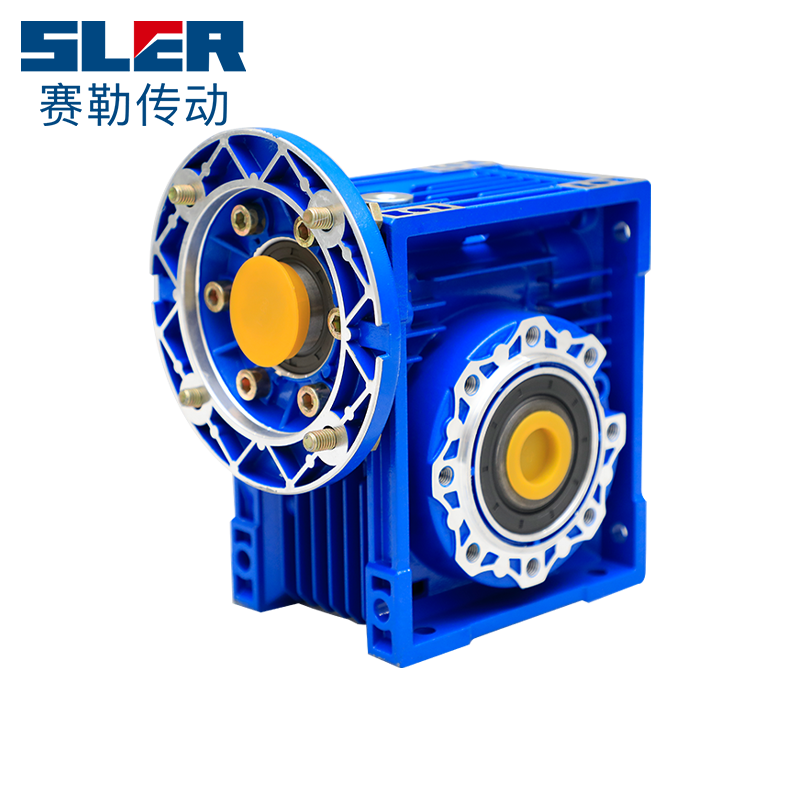
6. Micro-Pitting Resistance: Opt for lubricants specifically formulated to provide micro-pitting resistance, as micro-pitting can lead to increased noise levels.
7. Lubrication Interval: Maintain a regular lubrication schedule based on the manufacturer's recommendations to ensure consistent lubricant performance and prevent excessive wear that could lead to noise and vibration.
8. Oil Analysis and Monitoring: Implement an oil analysis program to monitor lubricant condition and detect any signs of contamination or degradation that could impact noise and vibration levels.
9. Lubrication Method: Choose a lubrication method that ensures even distribution of the lubricant across all gear teeth. Methods include oil bath lubrication, oil mist lubrication, and circulating oil systems.
10. Lubrication Quantity: Properly calculate the required lubricant quantity to ensure sufficient coverage and film thickness between gear teeth. Too much or too little lubricant can affect noise levels.
11. Gear Tooth Surface Treatments: Some lubricants are designed to complement specific gear surface treatments, such as coatings or hardening processes, enhancing lubrication effectiveness and minimizing noise.
12. Compatibility: Ensure the selected lubricant is compatible with the materials used in the gear system, including seals and gaskets, to prevent degradation or compatibility issues.
By choosing the right lubrication strategy and lubricant type, and by following proper maintenance practices, you can effectively reduce noise and vibration in worm gear speed reducers, resulting in smoother and quieter operation.