Reducing the positioning error of a helical gear motor to achieve precise motion control involves several strategies and techniques. Here are some key methods to minimize positioning error:
Select High-Precision Gear Motors:
Begin by choosing helical gear motors known for their precision and low backlash characteristics. Look for gear motors with tight manufacturing tolerances and high-quality materials.
Backlash Compensation Mechanisms:
Some helical gear motors are equipped with built-in backlash compensation mechanisms, such as split gears or dual-helical gears. These mechanisms automatically compensate for backlash, ensuring precise motion control. Consider gear motors with these features for applications where minimal positioning error is critical.
Reduced Backlash Gears:
Opt for helical gear motors designed with reduced backlash. Manufacturers may offer specific gear models designed for applications demanding high precision.
Tight Manufacturing Tolerances:
Ensure that the gear motor's components are manufactured to tight tolerances. Modern CNC machining and quality control processes can help achieve this. Components like gears, shafts, and bearings should be precisely manufactured.
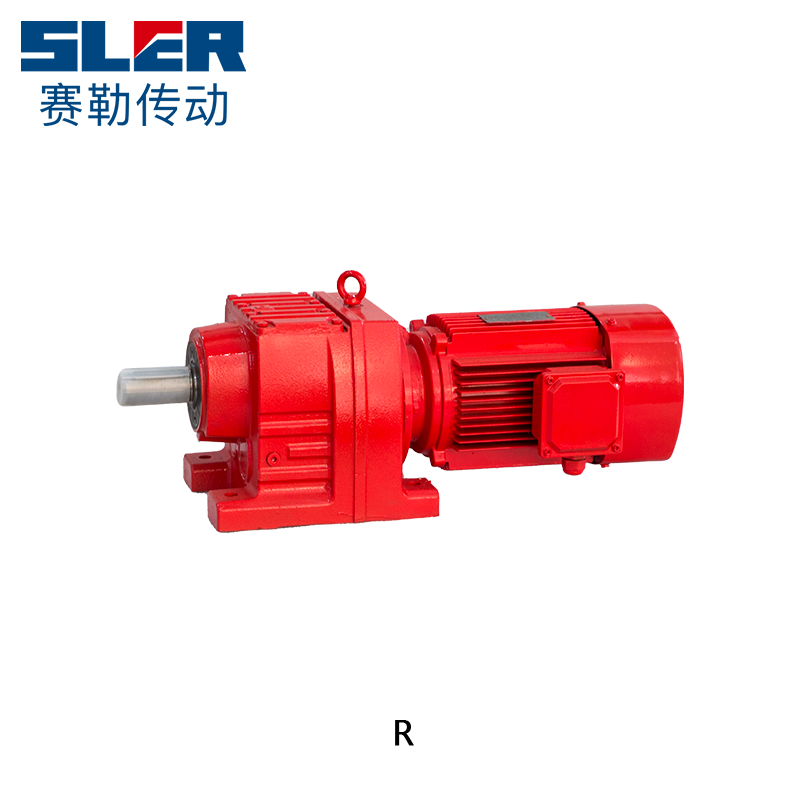
Optimal Gear Tooth Profile:
The gear tooth profile can significantly impact backlash. Helical gears with specific profiles, such as lead crowning and tip relief, can help minimize clearance between gear teeth and reduce backlash.
Preloading:
Apply a slight axial load or preloading to the gear mesh to reduce backlash. This can be achieved by incorporating spring-loaded or adjustable components in the gear motor.
Mounting and Alignment:
Properly mount and align the gear motor within the application to eliminate misalignment-induced backlash. Accurate alignment reduces positioning errors.
Closed-Loop Control Systems:
Implement closed-loop control systems that use encoders, resolvers, or other position feedback devices to actively compensate for any detected backlash or positioning errors. These systems adjust the motor's position in real-time to maintain the desired position accurately.
Advanced Control Algorithms:
Use advanced control algorithms that can predict and compensate for backlash based on previous motion patterns. These algorithms can help improve overall control accuracy, especially in systems with complex dynamics.
Minimize External Loads:
Ensure that the gear motor is not subjected to excessive external loads or forces that can introduce additional backlash or positioning errors. Properly design the mechanical system to distribute loads evenly.
Environment Control:
Maintain stable environmental conditions, especially temperature and humidity, as fluctuations can affect gear tolerances and cause variations in backlash.