Calculating the gear ratio of a parallel shaft helical gear motor plays an important role in engineering and mechanical design. This quantitative relationship between the number of teeth of the driving and driven gears fundamentally determines the speed and torque transmission characteristics within the mechanical system. By deriving the gear ratio, engineers can understand how many revolutions the driven gear makes compared to the driving gear.
For parallel-axis helical gear motors, the gear ratio directly affects the output speed of the motor and the torque applied to the load. Selecting the optimal gear ratio is critical to tailoring motor performance to the specific requirements of the application. Gear ratio defines the trade-off between speed and torque, allowing engineers to tailor system output to meet the needs of different industrial processes.
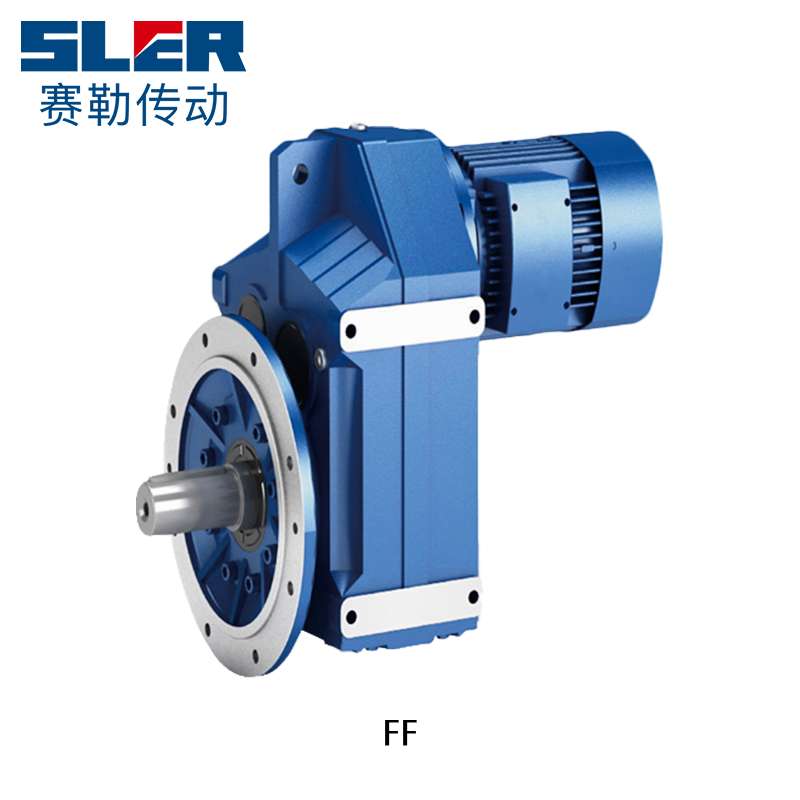
Furthermore, the gear ratio plays an important role in increasing or decreasing the speed produced by the motor, allowing it to effectively adapt to different operating scenarios. This is a key parameter for the overall efficiency and functionality of gear motors in the wider machinery sector. Accurate gear ratio calculations are critical to achieve the required power performance, avoid motor overload or underutilization, and ensure seamless integration into complex mechanical systems.
In summary, calculating the gear ratio of a parallel-axis helical gear motor is a fundamental step in engineering design, guiding the selection and customization of gear systems to achieve optimal speed and torque characteristics for various industrial applications. This calculation is critical to tailoring motor performance to specific operating needs and ensuring efficiency, reliability and seamless integration in complex mechanical systems.