Helical bevel gear motors adopt a variety of strategies and technical means when balancing mechanical strength and lightweight requirements.
Material selection: First of all, in terms of material selection, helical bevel gear motors tend to use high-strength, lightweight materials, such as aluminum alloy, titanium alloy or high-strength steel. These materials can not only provide sufficient mechanical strength, but also enable lightweight motors, thus improving overall performance.
Optimize structural design: Secondly, by optimizing structural design, lightweight can be achieved while ensuring mechanical strength. For example, the design of helical gears can use advanced tooth profile optimization technology to reduce stress concentration and improve load-bearing capacity. At the same time, through reasonable structural layout and size optimization, unnecessary weight can be reduced and overall efficiency improved.
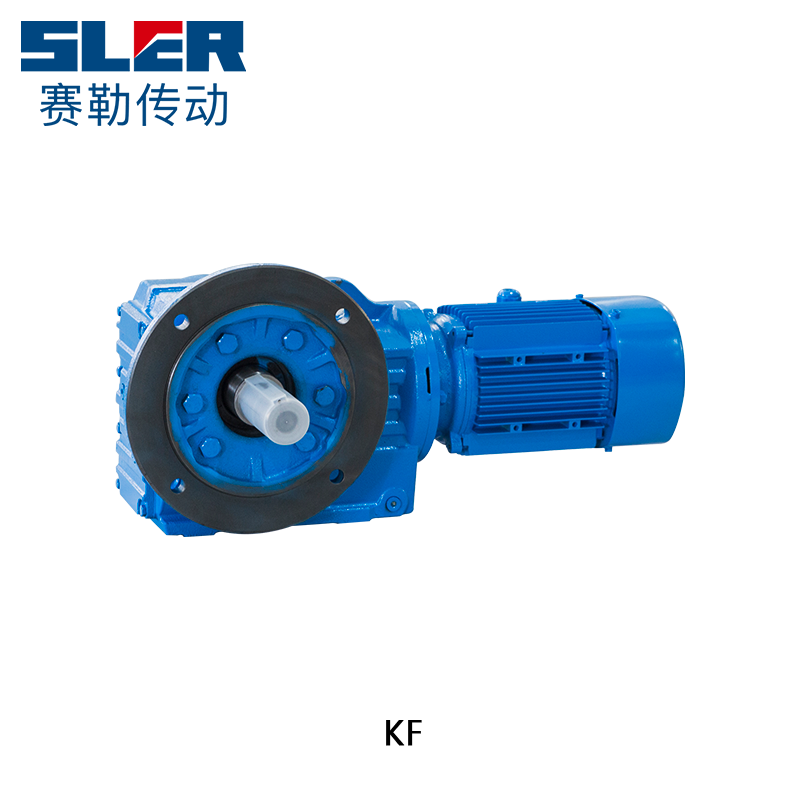
Heat treatment process: In addition, heat treatment process is also an important means to balance mechanical strength and lightweight requirements. By controlling the heat treatment process of the material, its mechanical properties and corrosion resistance can be improved, thereby reducing weight while ensuring mechanical strength.
Advanced manufacturing technology: With the continuous advancement of manufacturing technology, helical bevel gear motors can adopt more advanced processing methods, such as CNC machining, laser cutting, etc., to improve processing accuracy and efficiency. These technologies ensure precise fit of components and increase mechanical strength while reducing material waste and weight.
Simulation analysis and optimized design: During the design process of helical bevel gear motors, simulation analysis technology can be used to evaluate and optimize the design plan. Through comparative analysis of different design solutions, the best balance point can be found, that is, achieving maximum lightweighting while meeting mechanical strength.